Win With Quality. Conquer Compliance.
Bringing a medical device to market is like tournament chess—every move counts. With Rook, you gain expert guidance to navigate complexities and avoid costly delays.
Need Help Navigating the Quality System for the First Time?
Rook’s quality consultants will create a custom QMS for your company that is both efficient and easy to maintain. Our systems are audit ready and continually updated to ensure compliance.

300+ of the world’s leading MedTech companies trust RookQS:
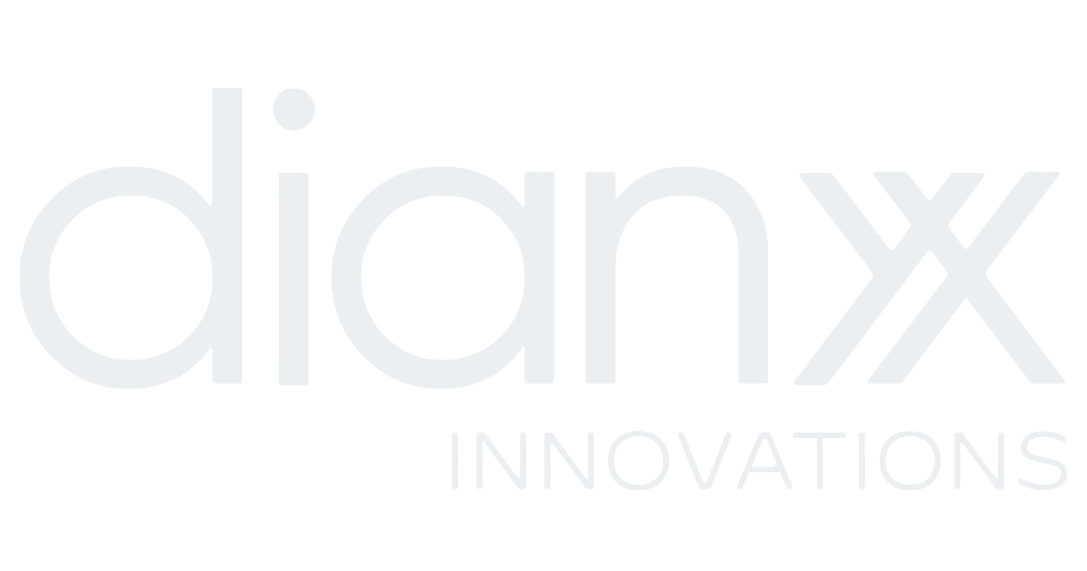
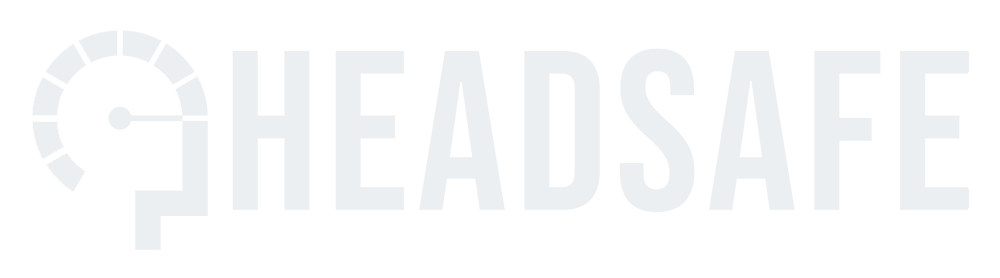
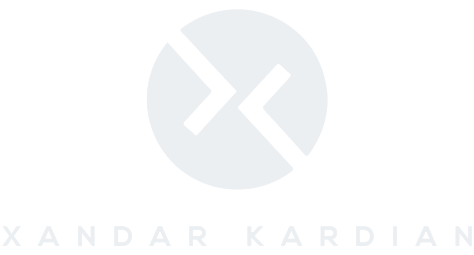
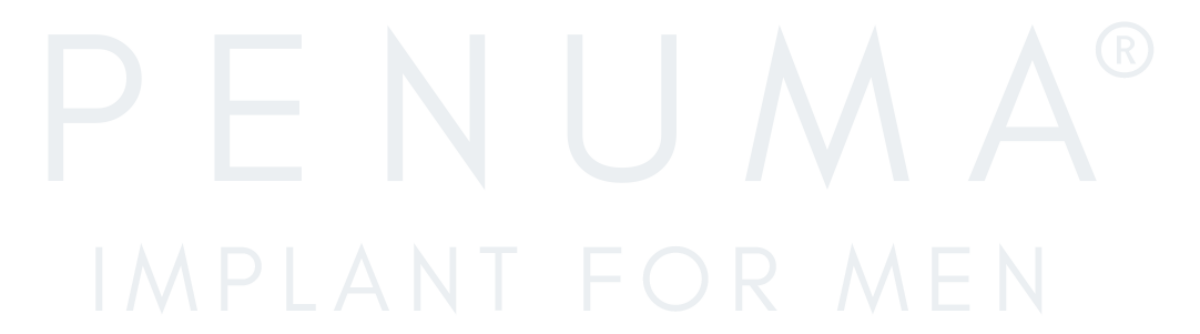
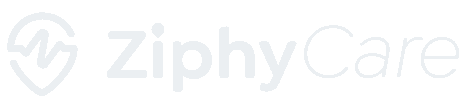

Struggling With the Complexities of Risk Management?
Rook will work with your company to develop a comprehensive risk management platform for products and processes, including the use of PHAs, FMEAs (process, use, design, and software).
Realizing the Devil’s In The Documentation?
If you didn’t document it, it didn’t happen (as far as the FDA and other regulatory bodies are concerned). Rook helps clients compile and maintain Quality Records documents that detail compliance history.

Our Solutions
.png)
Featured Resources

Testimonials
RookQS helped us with our quality services from inception, assisting us to scope and instantiate a compliant quality management system. The level of the service and support we’ve received has been outstanding, and I have no hesitation recommending them to other clients in our medical device industry.
Dr. Adrian Cohen, CEO and Founder
Headsafe
Dianyx Innovations engaged RookQS to support our efforts in pursuing 510k approval for our flagship product- a technology-enhanced sleep appliance (t.e.s.a.) After working with a previous FDA consultant, Rook’s experience, professionalism, and process-driven approach were refreshing to say the least. RookQS quickly aided in preparing Dianyx for pre-submission – developing the correct documentation, and supporting our team in the compilation while interfacing with the FDA to schedule the meeting. I would recommend RookQS to start-ups and established companies for support in their journey towards regulatory approval.
Rob Kibler, CEO
Dianyx Innovations
In 2022, recognizing the need for FDA compliance for ZiphyCam, we sought expert advice. The personable and knowledgeable RookQS team stood out among consultants, leading us to choose them. Their assistance in implementing and maintaining our QMS for ZiphyCam was seamless. Their willingness to share expertise in an accessible manner has made our partnership enjoyable. We’re extending our collaboration with Rook to include the ZiphyKit. I strongly endorse RookQS for any company seeking trustworthy, personable, and genuine subject matter experts.
Laura Gerety, SVP of Technology Operations
ZiphyCare
I am immensely grateful for the exceptional support provided by the RookQS team during the implementation of our QMS at Xandar Kardian. Their steadfast dedication and proficiency in navigating the complexities of QMS in a startup environment, coupled with their seamless collaboration across different time zones, have significantly accelerated our preparations for the impending MDSAP audit. The team’s expertise in simplifying intricate processes, prompt delivery of a detailed Gantt chart, and meticulous documentation through meeting minutes and charts have set a commendable benchmark for our vendors. I confidently recommend RookQS to any organization in need of reliable and knowledgeable partners, as their invaluable contribution has greatly impacted our QMS implementation success at Xandar Kardian.
Manju Anand, VP Operations
Xandar Kardian
The Rook team has been spectacular. They are very responsive and detail-oriented. The most positive feedback I’ve heard is from FDA and ISO inspectors. One ISO inspector said that as a result of Rook’s work, the Stage 1 audit was one of the best she’s reviewed in 10 years. An FDA inspector was similarly complimentary, saying the Rook team was deeply knowledgeable and professional. I couldn’t recommend Rook more. I think they’re phenomenal and have been a blessing for our company.
Jonathan Elist, CEO
Penuma
