Design History File (DHF)
What is a Design History File (DHF)?
A Design History File (DHF) is a comprehensive documentation of the medical device design and development process. It ensures compliance, provides traceability, facilitates communication, supports continuous improvement, and aids in audits and inspections. The DHF is a written record that outlines every decision, specification, change, and approval made during the design process.
Why is a DHF Important?
The DHF is crucial for regulatory compliance. It provides a detailed account of the design process, including the rationale behind design decisions. It helps regulatory bodies understand the device’s development and safety considerations, ensuring that the device is both safe and effective.
Key Elements of a Design History File
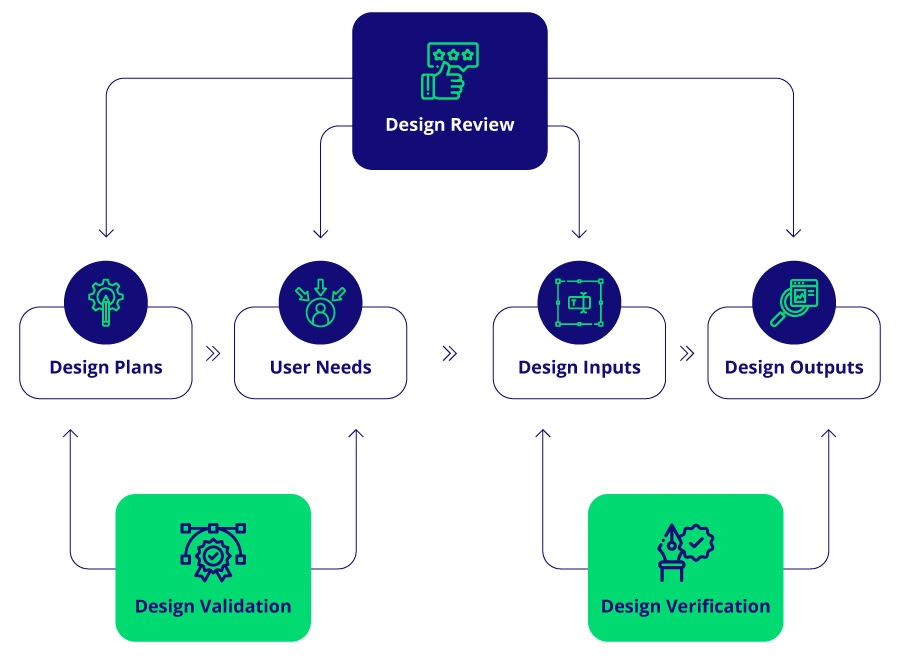
- Design Plans: Detail the steps to develop the device, including design reviews, team members, device purpose, and company goals.
- User Needs: Document the requirements and expectations of end-users, ensuring the product is safe, effective, and fit for its intended use.
- Design Inputs: Specify the device’s requirements derived from user needs and regulatory standards.
- Design Outputs: Include the design process’s results, such as drawings, specifications, and manufacturing processes.
- Design Review: Record formal reviews at various design stages to ensure compliance with specified requirements.
- Design Verification: Provide evidence that design outputs meet design inputs.
- Design Validation: Confirm that the final product meets user needs and intended uses.
DHF vs. DMR vs. DHR: What’s the Difference?
- DHF (Design History File): Documents the design process, choices, and testing.
- DMR (Device Master Record): Describes how the device is manufactured, including work instructions and procedures.
- DHR (Device History Record): This record keeps track of the devices produced, including labels, lots, and other relevant information.
Design History File (DHF) | Device Master Record (DMR) | Device History Record (DHR) |
---|---|---|
User requirement specifications | Process & instrumentation diagram | Production Records |
Validation activities | Material of construction details | Quantity Manufactured |
Software architecture | Components details | Quantity released for distribution |
Component drawings | Manufacturing details | Acceptance record |
Risk analysis | Packaging details | Non-conformance reports |
System tests | Shelf-life details | Lot & serial number |
Regulatory Requirements for DHF
FDA Requirements
The FDA mandates that Design History Files (DHF) include various elements. These elements are design inputs, design outputs, design reviews, verification testing, validation testing, design transfer, and documentation of design changes. Each component ensures the product development process is well-documented and adheres to 21 CFR 820.30 quality system regulations.
For more detailed guidelines, refer to the FDA’s guidance on Design History Files.
ISO Requirements
ISO standards require comprehensive design and development documentation within the DHF. This includes planning, design inputs, design outputs, design reviews, verification, validation, change management, and risk management. These steps are crucial for maintaining quality and ensuring the final product meets all necessary safety and performance criteria.
Best Practices for Managing Your DHF
- Start Early and Maintain It: Initiating DHF documentation early ensures compliance with regulatory laws, traceability, comprehensive risk management, and complete documentation.
- If in Doubt, Document It: Thorough and proactive documentation throughout the design and development process is essential.
- Ensure Traceability: Comprehensive documentation enhances traceability and accountability, linking every decision and change for regulatory compliance and project success.
Create and Maintain Your Medical Device DHF
RookQS’ team of experienced, certified quality engineers will help you create and maintain your medical device Design History File (DHF). Rook Quality Systems offers a comprehensive set of DHF templates specifically designed for software as medical devices.
DHFs for Software-Based Medical Devices
Key components include Software Requirements Specifications, Software Design Description, Software Development Plan, Software Test Plan, Software Verification and Validation Plan, Risk Management File, Configuration Management Plan, Release Notes, and Traceability Matrix.
Prepare Your DHF for an FDA Audit
Partner with Rook Quality Systems for an internal audit to identify gaps and ensure preparedness for an FDA audit.
Common Pitfalls and How to Avoid Them
Common mistakes include starting the DHF late, incomplete documentation, lack of traceability, inconsistent updates, poor document control, insufficient design reviews, ignoring risk management, and overlooking regulatory requirements. Recognizing these pitfalls and implementing solutions ensures a comprehensive and compliant DHF.
Contact Rook Quality Systems for expert assistance in managing your Design History File.