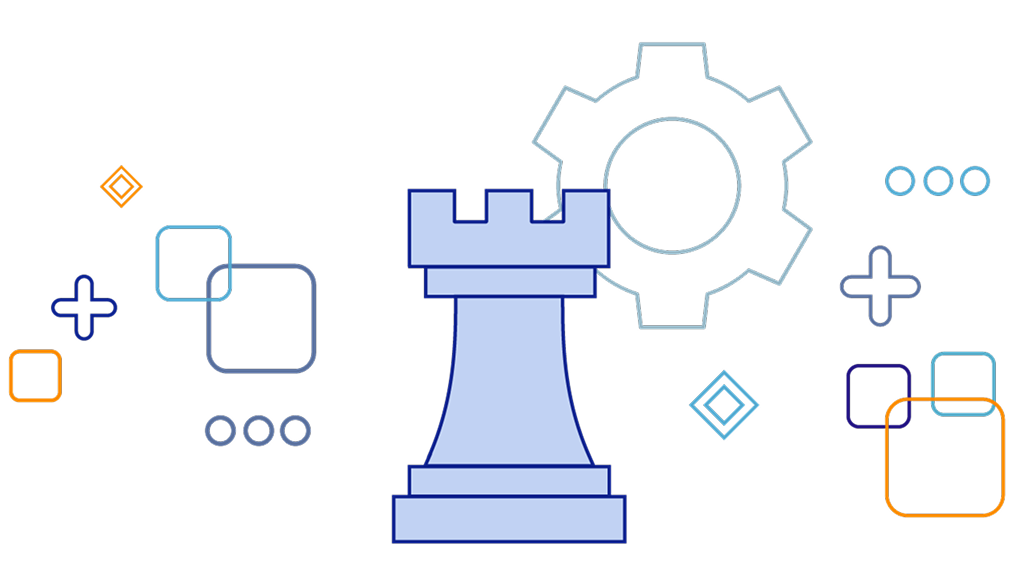
Quality Systems Management
Unsure of how you’ll manage a QMS after its creation? Our expertise does not end at initial QMS creation and implementation. RookQS has a decade of experience managing the quality system for a wide range of medical device, SaMD, and IVD companies. Whether you have an existing QMS and no one to manage it, or you are considering a QMS from RookQS and are hesitant to commit resources to managing it, we have an expansive team of engineers to dedicate to your QMS Management.
Expert Quality Systems Managers
Once paired with one of Rook’s experienced quality team, you will have quality personnel dedicated to your company. Early on, your dedicated quality manager and engineers are available to help with design and risk quality documentation, supplier qualification, QMS training management, and other pre-market QMS activities. When your company reaches the post-market phase, you can count on continued support from Rook’s engineers for activities including nonconformance management, CAPA management, customer feedback management, internal and supplier audits and more. Many companies struggle with the day-to-day questions and problems that pop up when managing a quality system; our team will assist with dedicated support and quick communication to ensure that you maintain complete confidence in your QMS.
Have a quality manager, but need quality support? At RookQS, we’ve seen first hand just how many resources it requires to get a med device company off the ground. We would be honored to share our experience and expertise and collaborate with you and your management team under your established procedures.
What is a Quality Management System (QMS)?
A Quality Management System(QMS) is based on the requirements of the US Quality System Regulation (QSR) 21 CFR 820, ISO 13485:2016 in order to demonstrate its ability to provide medical devices that consistently meet defined customer and regulatory requirements and its determination to enhance customer satisfaction
Elements of a Quality Management System
- Policies– High level documents concerning the procedures
- Standard Operating Procedures (SOPS) – Documents that describe the process flow of how to conduct a certain quality event
- Forms– the templates to fill in when an event needs to be performed
- Record– a form that has been completed and needs to be stored
- DHF– complied documents that describe the medical device
What Does a Quality System Manager Do?
A Quality Manager (QM) builds the QMS, DHF, and completes a risk analysis. They document any complaint, opens corrective and preventive actions, conducts post market surveillance, data analysis, line extensions, supplier evaluations, and other changes within the organization.